(1) Power System: Diesel vs. Electric – Matching Working Conditions
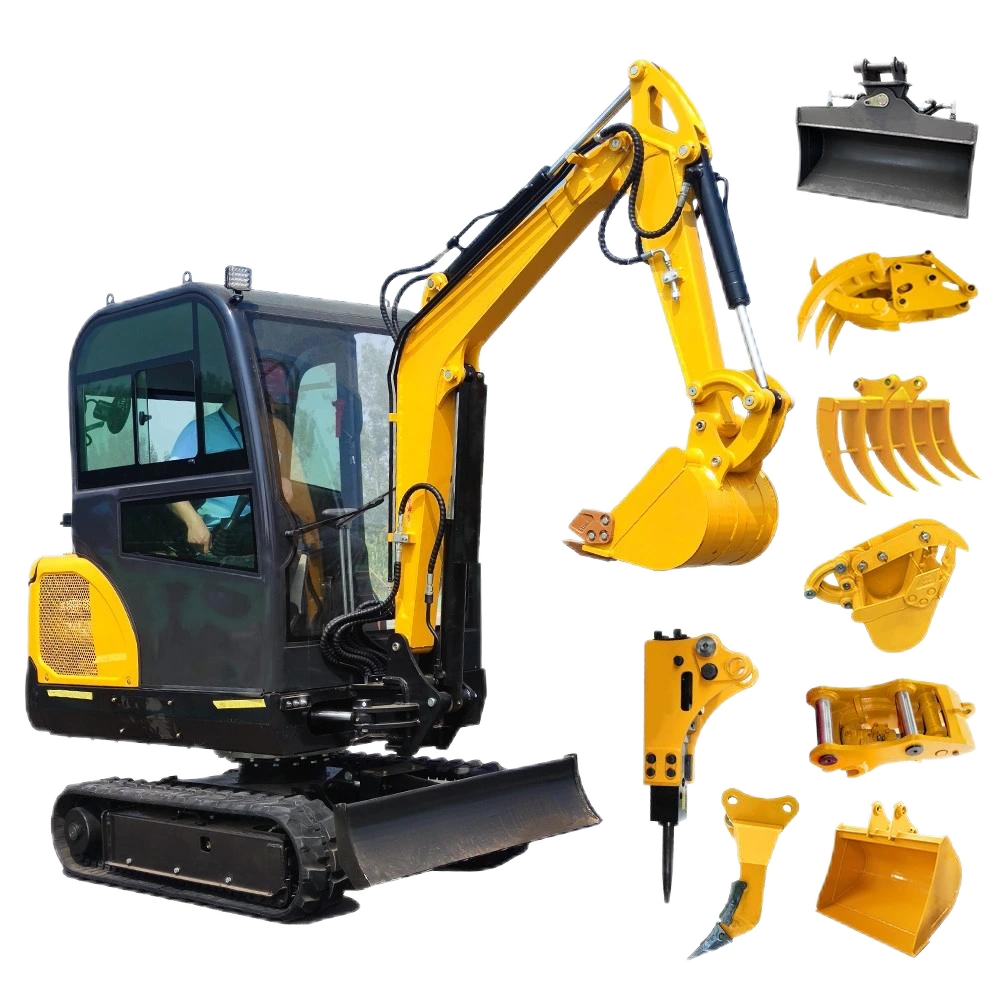
Diesel engines, with their high-torque characteristics, are suitable for heavy-duty scenarios such as mining and heavy infrastructure. For example, Cummins engines have a power reserve of over 30%, offering stronger stability in high-intensity operations like rock crushing. Electric motors, meanwhile, become the first choice for urban municipal projects and indoor demolition due to their zero emissions and low noise. Lithium-battery models have a battery life exceeding 8 hours and support fast charging, meeting the needs of high-frequency, short-distance operations.
Variable piston pumps combined with load-sensitive valves automatically adjust flow according to excavation resistance, saving over 20% energy compared to traditional fixed-flow systems. The hydraulic system has a response time of <0.3 seconds, with a 40% improvement in composite movement coordination. Fine leveling operations have an error ≤5mm, significantly reducing manual correction costs.
Standard GPS remote monitoring systems track equipment location, fuel consumption, and fault codes in real time, supporting remote locking for anti-theft purposes. High-end models integrate AI visual recognition to automatically avoid obstacles in the work area, and with electronic fence functionality, reduce accident risks by 60%.
The boom structure is designed using the "load coefficient method." For example, the arm bending strength of a 20-ton excavator is ≥350MPa. Combined with reinforced bucket teeth (hardness HRC55+), the digging force is 15% higher than conventional models. A mining case shows that in shale mining, the daily processing capacity reaches 2,000 tons, with a 25% efficiency improvement over similar products.
Engine blocks are cast from boron steel alloy, improving corrosion resistance by 50% and adapting to high-humidity and high-dust environments. Travel motors are equipped with a three-stage filtration system, maintaining hydraulic oil cleanliness at NAS 1638 Class 8 and extending seal life to over 5,000 hours.
Electronic control common rail technology combined with an intelligent power matching system automatically adjusts engine speed according to load, saving 18% fuel compared to mechanical pump models. data from a logistics park shows that during 8 hours of daily operation, fuel consumption is 1.2L/h lower than competitors of the same tonnage, saving over ¥20,000 in annual fuel costs.
The suspended cab is standard with silicone oil shock absorbers, achieving a vibration attenuation rate of 70% and noise control below 78dB. The multi-function control handle integrates 12 operational functions, allowing composite movements with fingertip control. Combined with an electrically heated seat (suitable for -20°C environments), winter operation comfort is increased by 50%.