I. Electric Forklifts: Redefining Industrial Handling Paradigms
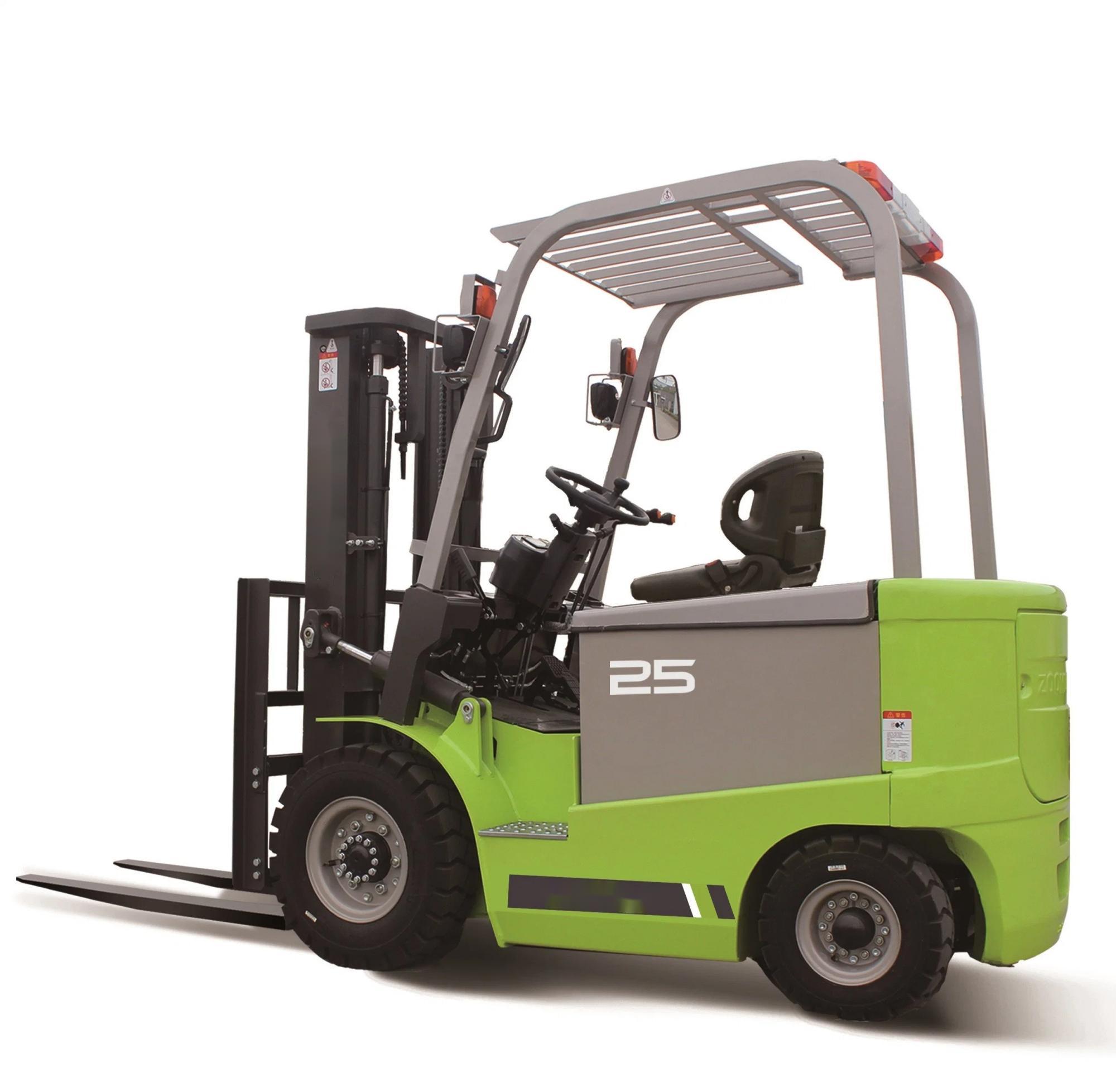
Powered by batteries and driven by motors for travel and hydraulic systems,
electric forklifts enable cargo loading/unloading and short-distance transportation. Unlike internal combustion forklifts, their core advantages lie in
zero exhaust emissions,
low noise (operation noise ≤70dB), and
energy conversion efficiency exceeding 80%—aligning with global environmental imperatives under the "dual carbon" goals. With the maturity of transistor controller (SCR/MOS tube) technology, electric forklifts have seen comprehensive improvements in battery life, control precision, and durability. With a load capacity ranging from 1.5 to 10 tons, they have become the mainstream choice for industries such as warehousing, manufacturing, and retail.
- Counterbalance Type: Suitable for outdoor heavy-duty handling (3-10 tons load capacity, 8-10 hours battery life for lithium-ion models);
- Reach Type: Specialized for narrow aisles (minimum aisle width 1.6m, lifting height up to 10m);
- Warehouse Type: Primarily electric pallet trucks and stackers, focusing on light-duty efficiency for e-commerce warehousing and sorting;
- Special Type: Customized models like explosion-proof forklifts (for chemical environments) and cold storage forklifts (operating at -30°C).
- Zero Emissions: No CO or NOx emissions, meeting the needs of cleanliness-sensitive industries like food, pharmaceuticals, and electronics;
- Low Noise: Operation noise reduced by 40% compared to internal combustion forklifts (≈75dB vs. 110dB), improving workplace comfort;
- Energy Efficiency: Electricity costs per hour are only 1/3 of fuel forklifts. With time-of-use pricing strategies, operational costs are further minimized.
- Precise Control: Electric signal-controlled steering, acceleration, and braking, with a minimum turning radius of 1.2m, improving passability in narrow spaces by 30%;
- Rapid Response: Instant torque output from DC motors enables a full-load lifting speed of 300mm/s, enhancing efficiency by 20% compared to traditional models;
- Intelligent Aids: Standard features include battery monitoring and anti-collision sensors. High-end models support automatic charging navigation (AGV functionality) to reduce manual intervention.
- Simple Maintenance: 70% fewer motor components than internal combustion engines, no need for oil or filter changes, reducing annual maintenance costs by 60%;
- Battery Upgrades: Lithium-ion batteries offer a cycle life exceeding 4,000 times (vs. 500 times for lead-acid batteries), support fast charging (80% in 1 hour), and extend daily operation to 12 hours;
- Policy Dividends: Governments in many regions offer purchase subsidies for electric forklifts (e.g., Shenzhen provides up to 30% per unit) and exempt carbon emission taxes during use, ensuring long-term cost-effectiveness.
- Stable Design: Low-center-of-gravity layout + wide-view mast reduces rollover risk by 50%;
- Braking System: Dual protection from electromagnetic and mechanical brakes, with emergency braking distance ≤2.5m (unloaded);
- Ergonomics: Suspension seats, adjustable steering wheels, and integrated control handles reduce driver fatigue and enhance 8-hour operational comfort.
In e-commerce warehouses, electric reach forklifts can complete high-position stacking (up to 12m) in 1.8m narrow aisles, achieving precise cargo location with WMS systems; electric pallet trucks handle the "last 100 meters" of transportation, supporting integration with automated conveying lines to improve inventory efficiency by over 30%. A typical case: JD.com’s Asia No. 1 Warehouse uses 500 electric forklifts to keep sorting error rates below 0.1%.
In automotive factories, electric counterbalance forklifts transport heavy components like engines and gearboxes, with low-temperature-resistant models operating stably in -20°C workshops; in 3C electronics production lines, explosion-proof electric forklifts meet safety requirements for lithium battery workshops, avoiding spark-related risks. Data shows that introducing electric forklifts has shortened material turnover cycles in manufacturing by an average of 25%.
- Cold Chain Logistics: Cold storage-specific electric forklifts are equipped with low-temperature-resistant batteries (maintaining battery life at -30°C) and corrosion-resistant stainless steel bodies, addressing 续航 and maintenance challenges in cold chain scenarios;
- Explosion-Proof Fields: Explosion-proof electric forklifts used in the chemical industry are ATEX-certified to eliminate sparks, ensuring safety in flammable and explosive environments;
- Indoor High-Precision Scenarios: Pharmaceutical warehouse picking forklifts are equipped with weighing sensors and fork positioning systems to achieve 0.5mm-level precision control, protecting high-value drug packaging.
In 2023, China’s electric forklift sales reached 796,600 units, a year-on-year increase of 18%, accounting for 64% of total forklift sales; export volumes also rose, with annual demand growth of 20% in Southeast Asia and Europe. Policy-wise, the Air Quality Continuous Improvement Action Plan mandates that the electrification rate of non-road mobile machinery reach 30% by 2025, accelerating the replacement of internal combustion forklifts in ports, parks, and other scenarios.
- Power Innovation: Lithium-ion forklifts now hold over 60% market share, with battery life increased by 40% and charging time reduced to 1 hour. Some high-end models use hydrogen fuel cells for "5-minute battery swapping";
- Intelligent Transformation: AGV electric forklifts integrate laser navigation and IoT modules to support multi-machine collaborative operations with errors ≤10mm; remote monitoring systems track equipment status in real time, achieving 95% fault warning accuracy;
- Material Upgrades: All-aluminum bodies reduce weight by 30% compared to traditional steel structures, lower energy consumption by 15%, and enhance corrosion resistance for humid and salt-fog environments.